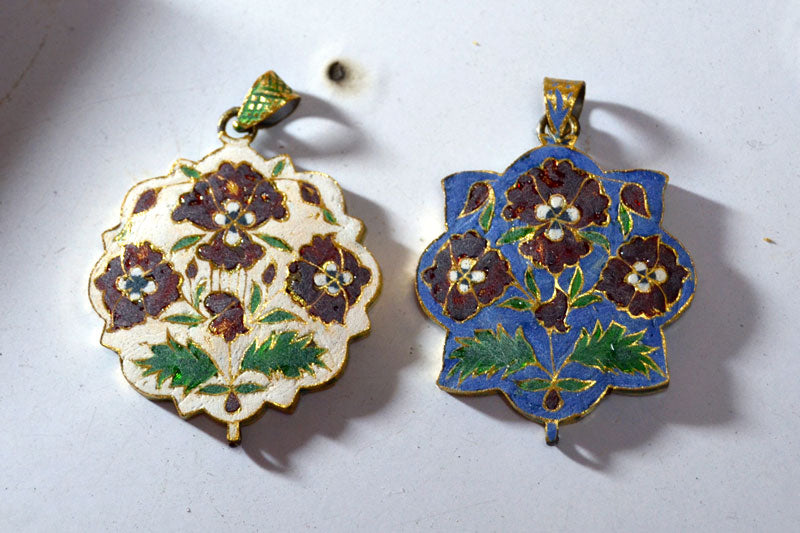
The Process Of How to Make Kundan Meenakari Jewelry
Share
Kundan-Meena is a unique technique of making jewelry by encrusting gold with precious and semi-precious stones (Kundan work) on one side and the art of colorful enamel work (Meenakari) on the reverse side. There are four steps to making any jewelry piece:
1) Ghadayi:-
'Ghadayi’ is a meticulous process that involves creating the foundational skeleton or framework of a jewelry piece, ensuring that every detail aligns with the chosen design. The first step in this process is to prepare thin gold strips using a rolling machine, which flattens the gold into uniform thickness. These strips are then cut into smaller pieces, coiled, and shaped according to the specific design requirements. The karigar, or artisan, carefully handles each strip with small tweezers and specialized tools to achieve the intended shape.
Once the individual components are shaped, they are carefully arranged on a wax board, which acts as a template. The wax board allows the artisan to replicate the design precisely, ensuring that each part of the framework fits together seamlessly. The pieces are then soldered together, a process where heat is applied to melt and fuse the gold, creating a single, solid structure, whether it's for an earring, pendant, or any other jewelry item.
After the soldering process, the jewelry piece often has a black residue, a byproduct of the heat and the flux used during soldering. This residue is carefully cleaned off using mild chemicals to restore the jewelry's smooth, shiny surface. After cleaning, the piece is thoroughly dried to ensure no moisture remains.
Next, the artisan heats lac (a natural resin) and pours it into the small creeks or cavities on the framework, which are meant to hold gemstones. The lac hardens as it cools, securing the gems in place once they are inserted. This process is crucial in ensuring the stones are held firmly and securely, completing the framework of the jewelry piece.
2) Khudayi:-
'Khudayi’ is the intricate process of engraving or etching designs onto the surface of a jewelry piece, whether on the front, back, or both. This step adds intricate details and artistic patterns, enhancing the overall aesthetic of the piece. The majority of the motifs used in Khudayi are floral or nature-inspired, but some designs also feature geometric patterns, providing a rich variety of visual appeal.
Exquisite engraving requires exceptional skill, a steady hand, high precision, and deep concentration from the artisan. The engraving is typically done using specialized tools, where the artisan carefully carves into the gold to create the fine details of the design. This delicate work demands both experience and artistry to ensure that the pattern is executed perfectly.
Throughout the engraving process, fine gold dust is produced as a byproduct. Rather than being discarded, this gold dust is collected and recycled, ensuring that no precious material is wasted and contributing to the sustainability of the process. The careful artistry involved in Khudayi transforms a simple jewelry piece into an intricate masterpiece, adding depth and texture to the design.
3) Meenakari:-
‘Meenakari’ is a decorative technique in jewelry-making that involves the application of enamel to create vibrant, colorful designs. This process is intricate and time-consuming, requiring great skill and precision. The colors traditionally used in Meenakari are red, green, blue, and white, which are chosen for their vibrant hues and ability to complement the gold base. When combined with the gold's color, this set of shades is known as ‘Panchranga,’ or the five-colored combination.
To apply the enamel, the artisan uses fine needles or spokes to carefully fill the engraved patterns on the jewelry piece with these colors. The process requires great attention to detail to ensure that the colors are applied neatly and precisely within the engraved lines.
Once the enamel has been applied, the jewelry piece must be fired multiple times, depending on the number of colors used. Each color requires a separate firing to ensure that the enamel properly bonds with the gold. Firing is typically done in an electric kiln, although some artisans may also use the coils of a domestic heater with a thin iron mesh to achieve the same result. This heating process fuses the enamel to the gold, ensuring the colors remain firmly in place.
After all the colors have been applied and fired, the piece is carefully scrubbed with a filer to accentuate the gold outline of the pattern. This step sharpens the contrast between the enamel and the gold, highlighting the design's details. To give the piece a polished finish, it is then boiled in a mild acid solution to bring out a beautiful sheen. Finally, the piece is passed on to the next karigar, who will carry out the stone-setting process to complete the jewelry.
4) Jadayi:-
‘Jadayi’ is the intricate process of gem setting, where gemstones are carefully positioned and secured within a jewelry piece. This method involves inserting a layer of gold foil between the stones and their mount to ensure a secure and stable setting. Commonly used gemstones in this process include diamonds, sapphires, emeralds, and rubies, which are selected for their beauty and brilliance.
To enhance the stones' depth and sparkle, a thin piece of silver foil is first placed beneath the stones. This helps to reflect light and adds to the overall brilliance and refraction of the stones, making them shine more vividly. The gemstones are then heated and placed on lac, a natural resin that holds the stones in place.
Once the stones are positioned, small pieces of 24-carat gold foil, which have been hammered to soften and make them malleable, are carefully set around the sides of the gemstones. This ensures the stones grip tightly and securely within their mount. The artisan uses fine, delicate tools to chisel the gold foil at precise angles, refining the setting and bringing out the fine details of each gemstone. This meticulous work enhances the stones’ inherent beauty and gives the jewelry piece a polished, sophisticated look.
Finally, the ornament is often adorned with additional hanging gems, adding extra shine and texture to the piece. The completed piece is then strung together on a wearable thread, making it ready to be worn and admired. The Jadayi process not only ensures the gemstones are securely set but also elevates their visual appeal, adding depth, color, and radiance to the jewelry.